Comprehensive Water and Wastewater Treatment Solutions for Dyeing Industries Using STP, ETP, WTP, RO, WWTP, and Recycling Systems

India's textile and dyeing sector plays a crucial role in its economic landscape, with dyeing being a vital component. The country houses thousands of small, medium, and large-scale dyeing units that cater to both domestic and international markets. These industries are primarily located in clusters such as Tiruppur, Ludhiana, Surat, and Ahmedabad.
In Maharashtra, industrial belts in Mumbai, Bhiwandi, and Ichalkaranji host several textile and dyeing hubs. These regions have witnessed steady growth due to policy support and proximity to raw materials and ports. However, water usage and pollution control remain key concerns in this segment, necessitating modern water treatment practices.
Water is used extensively for dye preparation, rinsing, washing, and chemical processing stages.
Dyeing processes are inherently water-intensive. Water is required at every stage—from preparing dyes and fixing agents to washing and finishing textiles. The quality of water also influences fabric color, texture, and chemical stability.
Soft water is especially preferred in dyeing, as hard water can alter chemical reactions, leading to inconsistent coloration. Water is also used for cooling machines, floor washing, and boiler operations, adding to the overall demand. This high dependency emphasizes the need for efficient usage and treatment systems.
Multiple stages, such as rinsing, washing, and chemical discharge, contribute to wastewater generation.
Wastewater originates from dye baths, rinsing tanks, de-sizing, and soaping processes. These streams carry unabsorbed dyes, surfactants, salts, acids, and heavy metals, making the effluent heavily polluted.
"In the dyeing industry, water is more than a utility—it's part of the product. From maintaining color consistency to removing residues, water plays a central role. Responsible sourcing and treating water not only preserve natural resources but also enhance the long-term sustainability and credibility of the business."
Other sources include machine cleaning and floor wash water that adds detergent and chemical waste. The variety and volume of effluents vary by fabric type, dye used, and batch size. Unchecked discharge pollutes water bodies and violates pollution norms, making proper treatment systems a necessity.
Effluents contain dyes, salts, alkalis, acids, heavy metals, and high chemical load.
Wastewater from dyeing units is typically high in Chemical Oxygen Demand (COD), Biological Oxygen Demand (BOD), total dissolved solids (TDS), and color. These effluents are challenging to treat due to their resistance to natural decomposition and intense coloration.
The water also contains chemicals like sodium hydroxide, acetic acid, hydrogen peroxide, surfactants, and azo compounds. Inadequately treated water can harm aquatic ecosystems and groundwater sources. Therefore, specialized treatment is essential to address these chemical complexities.
Multi-stage treatments like ETPs, neutralization tanks, and filtration units ensure effective pollutant removal.
Treatment typically begins with neutralization to adjust pH levels, followed by coagulation and flocculation to remove suspended solids and color. Primary clarifiers and oil separators are used to extract sludge and organic matter.
Secondary treatment includes biological processes like activated sludge or MBBR systems. Tertiary stages involve sand filtration, activated carbon filtration, and disinfection through UV or ozone. These systems ensure that treated water meets discharge norms or becomes suitable for reuse within the plant..
MBR, UF, and RO technologies enable effective water recycling and zero liquid discharge (ZLD)
Advanced technologies like Membrane Bioreactors (MBR), Ultrafiltration (UF), and Reverse Osmosis (RO) are now standard in modern dyeing plants. These help in removing micro-pollutants, colorants, and salts, making the water fit for reuse.
Automated control systems and SCADA monitoring ensure operational efficiency and real-time performance tracking. Many plants are moving towards Zero Liquid Discharge (ZLD), where every drop is treated and reused. This not only cuts freshwater dependency but also aligns with environmental mandates.
We deliver customized water treatment solutions designed for the dyeing and textile sector.
We specialize in providing end-to-end water and wastewater treatment systems for dyeing industries. Our expertise covers ETPs, STPs, WTPs, RO plants, and complete ZLD solutions. Each project is customized based on your fabric type, dyeing process, and discharge norms.
Our services include design, supply, installation, automation, and post-commissioning support. We also help with upgrades of older systems to meet new pollution control board requirements. We aim to help you stay compliant while optimizing operational costs and resource utilization.
Conclusion: Water Management is a Business Essential for Dyeing Industries
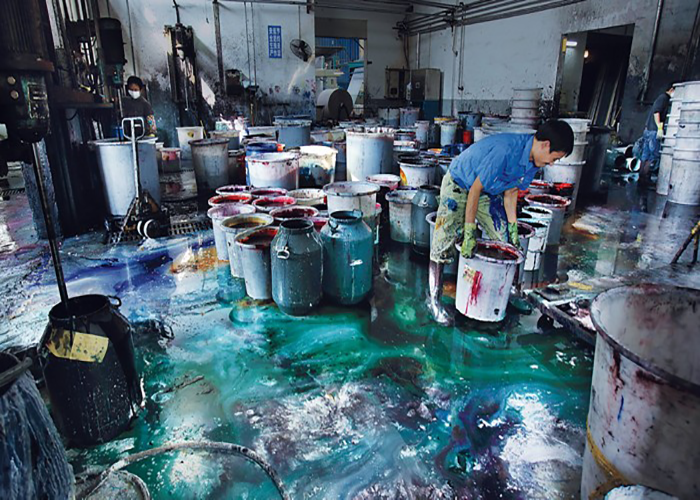
Conclusion: Water Management is a Business Essential for Dyeing Industries
The dyeing industry cannot function without water—but the way water is managed defines long-term success. With increasing regulatory pressure and shrinking water resources, investing in effective water treatment solutions is not just an option but a necessity.
From ETPs to RO systems and ZLD integration, adopting the right technology ensures environmental compliance, cost savings, and brand reputation. By working with a trusted water treatment partner, dyeing units can balance growth with responsibility.